Transfer's (manipulator's) use in the automotive industry
The amount of aluminum alloys in the materials used for the entire vehicle has increased year over year as a result of the growth of its automobile industry. As a result, sheet metal stamping processing advancement is accelerating. More and more automakers now view the usage of aluminum plate as a key strategy for increasing the green content of cars by gradually replacing the steel plate that makes up the body of the vehicle.
Currently, the majority of manufacturing lines for vehicle sheet metal stamping use automatic loading and unloading. Both high movement speed and high sheet metal transportation positioning precision are necessary for this automatic production line of car sheet metal stamping manipulators. The automated manufacturing line's sheet metal stamping transfer (manipulator) precisely moves the sheet into place in accordance with the sheet's parameters. Utilizing transfer (manipulator) for sheet metal stamping helps speed up production and maintain product quality for sheet metal stamping businesses.
A number of gantry supports are included in the truss of the truss transfer (manipulator), and the supports have beams attached so that the manipulator can be installed. A manipulator with three degrees of freedom is the truss transfer (manipulator). The horizontal movement component and the vertical movement component, respectively, each include gears and racks for transmission, and the gears and racks are arranged as helical teeth meshing with one another. The bottom of the vertical movement component is connected with the three-claw gripper.
The truss transfer (manipulator) is an entirely automatic industrial device based on the rectangular X, Y, and Z three-coordinate system. It uses three mutually perpendicular linear motions to modify the workpiece's station or to orbit it, among other things. Industrial controllers (such PLCs, motion controllers, single chips, etc.) are used to implement its control center. Following the controller's analysis and processing of the signals from various inputs (sensors, buttons, etc.), the controller. The servo motor can be used to respond fast and steadily thanks to its high efficiency, linear axes that run at a very high speed, minimum repeatability error, and capacity to reach high positions. Precision (μm level)
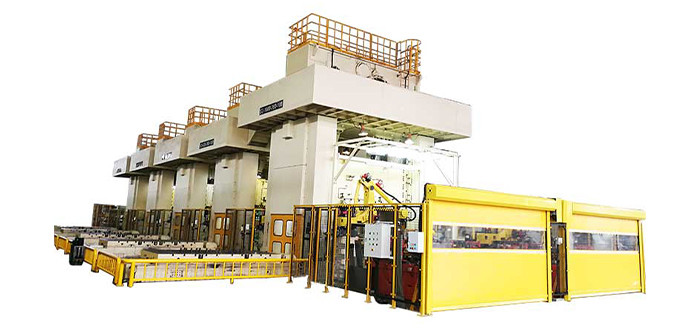
The truss transfer (manipulator) can work continuously for 24 hours a day without stopping for food, rest, or smoking, etc., maximizing manpower savings and enhancing the technical appearance of factory production. High accuracy Positioning precision can be as high as 0.02mm. To satisfy the demanding needs of the manufacturing process, it can achieve the flexible combination of several punching machines, automatic loading and unloading, and workpiece clamping with various degrees of freedom.