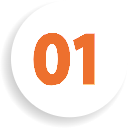
Pre-installation Planning
Our process begins with a detailed pre-installation assessment. We'll work closely with you to understand your production layout, existing equipment, and any specific requirements or constraints. Based on this information, we'll develop a customized installation plan that outlines the timeline, resource requirements, and steps involved. We'll also provide you with a clear breakdown of the costs associated with the installation and commissioning services.
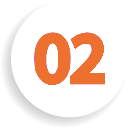
Equipment Delivery and Unloading
Our logistics team will ensure that your coil handling equipment is delivered to your facility safely and on time. Upon arrival, our technicians will carefully unload the equipment and conduct a visual inspection to check for any damage during transit. If any issues are found, we'll take immediate steps to resolve them before proceeding with the installation.
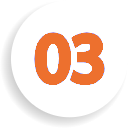
Installation and Setup
Our experienced technicians will then begin the installation process. They'll follow the pre-approved installation plan, carefully positioning the equipment and connecting all the necessary components. We'll ensure that the equipment is properly grounded and that all electrical and mechanical connections are secure. Throughout the installation, our team will maintain a clean and organized work area to minimize the risk of accidents and ensure a smooth process.
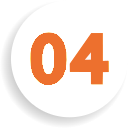
Commissioning and Testing
Once the installation is complete, we'll move on to the commissioning phase. Our technicians will power up the equipment and conduct a series of tests to verify its functionality. We'll check the operation of all components, including motors, sensors, and control systems. We'll also perform performance tests to ensure that the equipment is delivering the expected results in terms of speed, accuracy, and reliability. If any adjustments are needed, we'll make them promptly and retest the equipment until it meets our high standards.
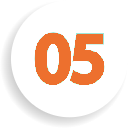
Training and Handover
After successful commissioning, we'll provide comprehensive training for your operators and maintenance staff. Our trainers will cover all aspects of equipment operation, safety procedures, basic maintenance, and troubleshooting. We'll also provide you with detailed documentation, including operation manuals, maintenance schedules, and spare parts lists. Once your team is comfortable with the equipment, we'll officially hand it over to you, confident that you have the knowledge and support to operate it effectively.