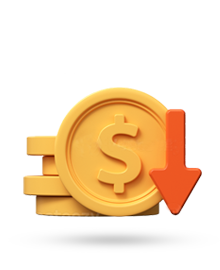
Complex Shape Cutting
- Traditional blanking methods often require multiple operations and custom dies, which are costly and time - consuming.
Handling for coil uncoiling, feeding, straightening and cutting into sheet metal in a seamless, automated process.
① Laser Power and Performance-The laser power is a crucial factor as it determines the line's ability to cut through different materials and thicknesses.
② Cutting Speed and Precision- Cutting speed directly impacts productivity
① Material Types- A Coil-fed Laser Blanking Line should be able to handle a wide variety of materials, including steel (carbon steel, stainless steel, etc.), aluminum, copper, brass, and various alloys.
② Material Thickness- Handle different material thicknesses is important. Consider the minimum and maximum thicknesses of the materials you are likely to work with in the future.
① Production Volume- A high volume or low volume production needs matters the Coil Laser Blanking Line you will choose.
② Production Rate- Calculate your required production rate in terms of the number of parts per hour or per day. Compare this with the rated production rate of the potential lines you are considering. Keep in mind that the actual production rate may be affected by factors such as material type, thickness, and the complexity of the parts being cut.
① Equipment Cost- The cost of the Coil-fed Laser Blanking Line itself is a significant factor. Prices can vary widely depending on the line's features, capabilities, and brand. Compare quotes from different manufacturers, but also consider the quality and reputation of the brand.
② Installation and Training Costs- Installation may require specialized tools and expertise, and proper training is essential to ensure that your operators can use the line safely and efficiently. Some manufacturers may include installation and training in the purchase price, while others may charge additional fees.
Our Coil-fed Laser Blanking Lines use advanced laser technology to cut intricate shapes directly from the coil, eliminating the need for dies and reducing setup times. For example, in the production of automotive parts with complex geometries, our lines can cut the parts with precision, ensuring a perfect fit.
Our Coil-fed Laser Blanking Lines optimize material usage by nesting parts more efficiently on the coil. The laser can cut parts closer together, reducing the amount of wasted material. This not only saves costs but also contributes to a more sustainable manufacturing process.
Our Coil-fed Laser Blanking Lines offer the flexibility to quickly switch between different part designs without the need for die changes. This makes them ideal for high - mix, low - volume production, allowing manufacturers to respond quickly to changing customer demands.
The DSF model Decoiler Straightener Feeder is normally play a important role in coil-fed laser blanking line.This coil handling equipment combines a feeder, straightener, and uncoiler into a single unit and has highly integrated operational management.
The metal coil or sheet is cut into the appropriate forms or blanks by using a high-power laser cutting machine. Computer numerical control (CNC) directs the laser beam to follow a predetermined cutting path, which is established by the intended pattern or design.
Stacking cutting products/stamping products automatically. When paired with a lifting platform and trolley, stacker can also move steel plates that need to be chopped and stacked neatly to the packaging area.
Our experienced technicians will install and commission the line at your facility. We'll ensure that all components are properly installed, calibrated, and tested before handing over the line to you.
We provide training to your operators and maintenance staff. Our training programs cover everything from basic operation to advanced troubleshooting, ensuring that your team can operate the line safely and efficiently.
We offer a range of maintenance services, including preventive maintenance, emergency repair, and spare parts supply. Our dedicated support team is available 24/7 to respond to any issues you may encounter, minimizing downtime and keeping your production running.
We are committed to help customers minimize production line downtime and improve metal stamping efficiency and save cost surely.
Our vision is to become become a global leader in metal stamping automation, driving industry more smart and efficient.
Committed to improving the efficiency of coil handling equipments and avoid material waste.
① Visual Inspection
② Cleaning
① Lubrication
② Tension Adjustment
① Alignment Check
② Electrical System Inspection
① Component Wear Assessment
② System Calibration
① Overhaul and Replacement
② Safety System Inspection
Answer: Coil-fed laser blanking lines are highly versatile and can process a wide array of materials. Commonly, they can handle various grades of steel, including carbon steel and stainless steel. Aluminum, with its different alloys, is also a suitable material, although special considerations might be needed due to its reflective properties. Copper, brass, and other non-ferrous metals are also within the processing range.
Answer: In most cases, coil-fed laser blanking lines can be integrated with existing production equipment. However, the extent of integration depends on various factors, such as the type of equipment you have, the communication protocols used, and the physical layout of your production area.
Answer: The production speed can vary significantly based on multiple factors. Material type and thickness play a major role; for example, thinner materials generally allow for faster cutting speeds compared to thicker ones. The complexity of the part being cut also affects the speed; simple shapes can be cut more quickly than intricate ones.
Cover decoiler, coil feeder, uncoiler cum straightener, decoiler straightener feeder etc.
Having provided the Tailor-made coil feeding lines since 2013.
Reliable service backup on pre-sales, sales consulting, after-sales.
Pls contact us fanty@sz-fanty.com for a detailed talk!