Review Top 10 Stamping and Cutting Industry Trends for 2024
When we talk about stamping automation, the stamping and cutting industry is experiencing rapid transformation, driven by technological advancements and shifting market demands. As we review 2024, several key trends are set to reshape the metal stamping sector, providing opportunities for businesses to improve efficiency, sustainability, and innovation. Let’s explore the top 10 trends that will dominate the stamping and cutting landscape this year.
Increased Automation and Robotics
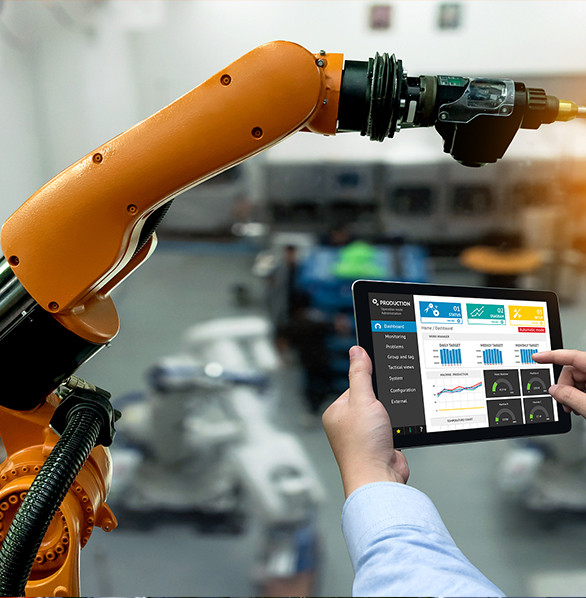
Automation and Robotics
Automation continues to be a game-changer in the stamping and cutting industry. With a focus on improving precision, reducing costs, and increasing productivity, businesses are increasingly adopting robotic solutions. Robots are particularly valuable for handling repetitive and dangerous tasks, allowing human operators to focus on more complex, value-added activities. Expect automation to play an even larger role in 2024, enhancing overall operational efficiency.
2. Advanced Materials for Greater Performance
The use of advanced materials like lightweight alloys and composites is rising. These materials offer superior strength and flexibility while helping to reduce component weight, which is crucial for industries like automotive and aerospace. These innovations contribute not only to performance but also to energy efficiency and sustainability, driving demand for lighter, stronger, and more sustainable products.
3. Digital Simulation and Modeling
As digital technologies advance, so too do simulation and modeling tools. These tools allow manufacturers to simulate and predict the outcomes of stamping and cutting processes, reducing the need for costly physical prototypes. By optimizing production parameters, companies can boost operational efficiency, minimize waste, and improve the overall design process.
4. High-Precision Cutting Techniques
Precision is more important than ever in industries like aerospace, electronics, and medical device manufacturing. Cutting methods such as laser cutting and water jet cutting are becoming increasingly accurate and efficient, allowing for complex and intricate cuts. These techniques are essential for producing high-quality, precise components, and their adoption is set to increase significantly in 2024.
5. IoT Integration for Smarter Operations
The Internet of Things (IoT) is revolutionizing the way companies monitor and optimize stamping and cutting operations. IoT-enabled sensors collect real-time data on machine performance, which helps to prevent breakdowns, optimize processes, and improve overall machine uptime. As connectivity improves, this trend will expand, enabling smarter factories and more efficient production lines.
6. Additive Manufacturing Enhances Stamping
Additive manufacturing, also known as 3D printing, is playing an increasingly important role in the stamping and cutting industry. In 2024, additive manufacturing will complement traditional stamping techniques by enabling the rapid and cost-effective production of customized tools, dies, and prototypes. This flexibility is especially beneficial for low-volume production and short-run manufacturing.
7. Ecology and Sustainability in Stamping
As environmental concerns grow, the stamping and cutting industry is focusing on reducing its carbon footprint. Companies are investing in sustainable practices, such as optimizing production processes to minimize waste, using recyclable materials, and adopting energy-efficient technologies. These efforts not only help businesses meet regulatory requirements but also resonate with environmentally conscious consumers and industries.
8. Ongoing Training and Skills Development
The rapid pace of technological change in stamping and cutting means that operators and engineers must continually upgrade their skills. In 2024, companies are placing greater emphasis on training programs to ensure staff are well-equipped to handle emerging technologies. This includes online courses, hands-on workshops, and partnerships with academic institutions to foster continuous learning and innovation.
9. Industry Collaborations for Innovation
Partnerships between manufacturers, research institutions, and technology providers are becoming more common. These industry collaborations allow businesses to leverage cutting-edge research and share knowledge on new techniques and technologies. Joint research projects are leading to breakthroughs in stamping and cutting methods, helping the industry stay ahead of the curve.
10. Customization and Production Flexibility
The growing demand for customized products is pushing companies to adopt flexible production methods. Stamping and cutting systems must be able to quickly adapt to varying designs and production volumes. In response, companies are investing in modular solutions and flexible production lines that allow them to accommodate a broader range of customer needs and production requirements.
Embrace Change to Stay Competitive for Fanty
To remain competitive in this rapidly evolving sector, we, Fanty, must embrace these trends and invest in the future of stamping and cutting technologies.
"FANTY" brand was established in 2013 with production base in Dongguan, Guangdong Province. At Fanty, we specialize in manufacturing metal stamping automation equipments and providing custom solutions that our clients can rely on. Our metal stamping automation equipments range includes high-quality decoiler machines, press feeders, press machines, transfers and also custom metal stamping automation solutions designed to boost production efficiency and precision for a variety of industries.
Our facility spans 45,000㎡ and includes 8 specialized assembly workshops staffed by a skilled team of 370 employees. In our Engineering Center, over 80 R&D technicians drive innovation and technical excellence.
Conclusion
The stamping and cutting industry in 2024 is defined by significant shifts toward automation, precision, sustainability, and customization. By adopting cutting-edge technologies like robotics, digital simulation, and advanced cutting methods, businesses can improve productivity, reduce costs, and create more sustainable products. Moreover, industry collaborations and ongoing skills development will play crucial roles in driving further innovation.