What Are Essential Considerations for Using a Roll Feeder in Punching Press Machines ?
In the realm of manufacturing, the efficiency and precision of punching press machines are paramount. One of the critical components that enhance the performance of these steel coil handling Equipments is the roll feeder. This article delves into the essential considerations for utilizing a roll feeders in punching press machine, ensuring optimal operation and productivity.
What Is A Roll Feeder ?
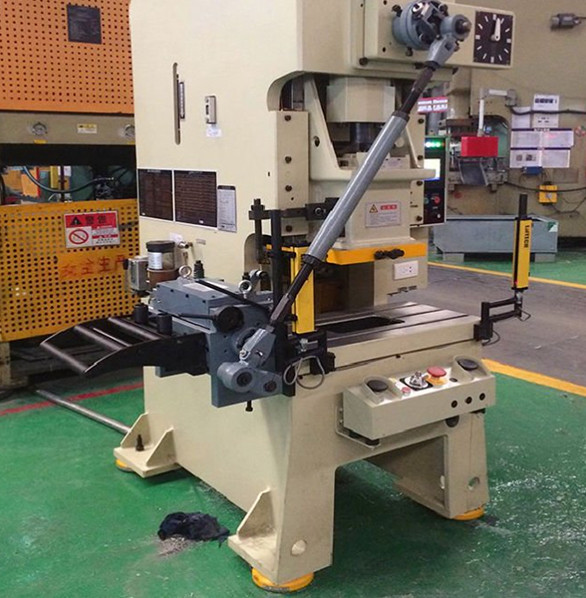
Understanding Roll Feeder
Roll feeder is a mechanical device designed to transport / feed steel coil through a punching press machine. It plays a crucial role in ensuring that the steel coil is fed accurately and consistently, which is vital for achieving high-quality punched products.
Types of Press Feeders
Mechanical Roller Feeders: These press feeders utilize gears and belts to move the material. They are known for their reliability and are suitable for various materials.
Pneumatic Air Feeders: Utilizing air pressure, these press feeders offer flexibility and are ideal for delicate materials that require gentle handling.
Servo-driven Feeders: These advanced press feeders provide precise control over the feeding process, allowing for adjustments in speed and position, which is essential for complex punching tasks.
Key Considerations for Implementation
Material Compatibility
Before integrating a roller feeder into a punching machine, it is crucial to assess the compatibility of the press feeder with the material being processed. Different materials, such as metals, plastics, or composites, may require specific feeder designs to ensure optimal performance.
Feed Rate Adjustment
The feed rate is a critical factor that influences the efficiency of the punching process. It is essential to adjust the feed rate according to the material thickness and type. A well-calibrated feed rate minimizes waste and maximizes productivity.
Maintenance and Upkeep
Regular maintenance of the roller feeder is vital for ensuring its longevity and performance. This includes:
Lubrication: Keeping the moving parts well-lubricated to reduce friction and wear.
Inspection: Regularly checking for wear and tear, especially on rollers and belts.
Calibration: Periodically calibrating the feeder to maintain accuracy in material feeding.
Integration with Punching Press Machines
The successful integration of a roller feeder with a punching machine requires careful consideration of the following:
Alignment: Ensuring that the feeder is correctly aligned with the punching mechanism to prevent jams and misfeeds.
Control Systems: Implementing advanced control systems that allow for real-time adjustments based on the punching machine's performance.
Benefits of Using Roller Feeders
Increased Efficiency
Roller feeders significantly enhance the efficiency of punching operations by providing a continuous and reliable feed of materials. This reduces downtime and increases overall productivity.
Improved Precision
With the ability to control the feed rate and alignment, roller feeders contribute to higher precision in the punching process, resulting in better-quality products.
Reduced Labor Costs
Automating the feeding process with roller feeders reduces the need for manual handling, thereby lowering labor costs and minimizing the risk of human error.
Conclusion
Incorporating a roller feeder into a punching press machine is a strategic decision that can lead to enhanced efficiency, precision, and cost savings. By considering material compatibility, feed rate adjustments, maintenance, and integration, manufacturers can optimize their punching operations and achieve superior results.
Contact us fanty@sz-fanty.com for a quotation now !