What Are the Latest Innovations in Coil Feed Lines for the Automotive Industry?
As the automotive industry continues to evolve, one of the most important aspects of manufacturing is improving the efficiency, precision, and sustainability of production lines. Coil feed line is an essential component in stamping processes, feeding metal coils into production machinery for the creation of automotive parts. As manufacturers strive for faster production speeds, reduced waste, and increased product quality, several innovations in coil feed lines have emerged to address these challenges. In 2025, trends such as servo-driven coil feeders, IoT-enabled monitoring, and energy-efficient systems are shaping the future of automotive manufacturing.
For those in the automotive industry searching for coil feed lines, servo-driven feeders, and automotive stamping technologies, this article will explore the cutting-edge developments in coil feeding systems and how they are revolutionizing automotive production.
Key Innovations in Coil Feed Lines for the Automotive Industry
1. Servo-Driven Coil Feeders for Precision and Efficiency
One of the most notable advancements in coil feed lines is the development of servo-driven coil feeders. Unlike traditional mechanical feeders, which rely on fixed speeds and mechanical adjustments, servo-driven systems offer precise control over feeding speeds and tension, ensuring a smoother operation. This innovation allows manufacturers to handle a wider range of materials, including thinner gauges and high-strength alloys, with minimal adjustments.
Benefits of servo-driven systems:
* Improved feeding accuracy, reducing material wastage and enhancing product quality.
* Higher flexibility to handle varying coil thicknesses and sizes.
* Increased speed and throughput, without compromising precision.
With servo-driven technology, manufacturers can adapt more easily to different production requirements, which is essential for automotive manufacturing where the complexity of parts continues to increase.
2. IoT-Enabled Monitoring for Real-Time Insights
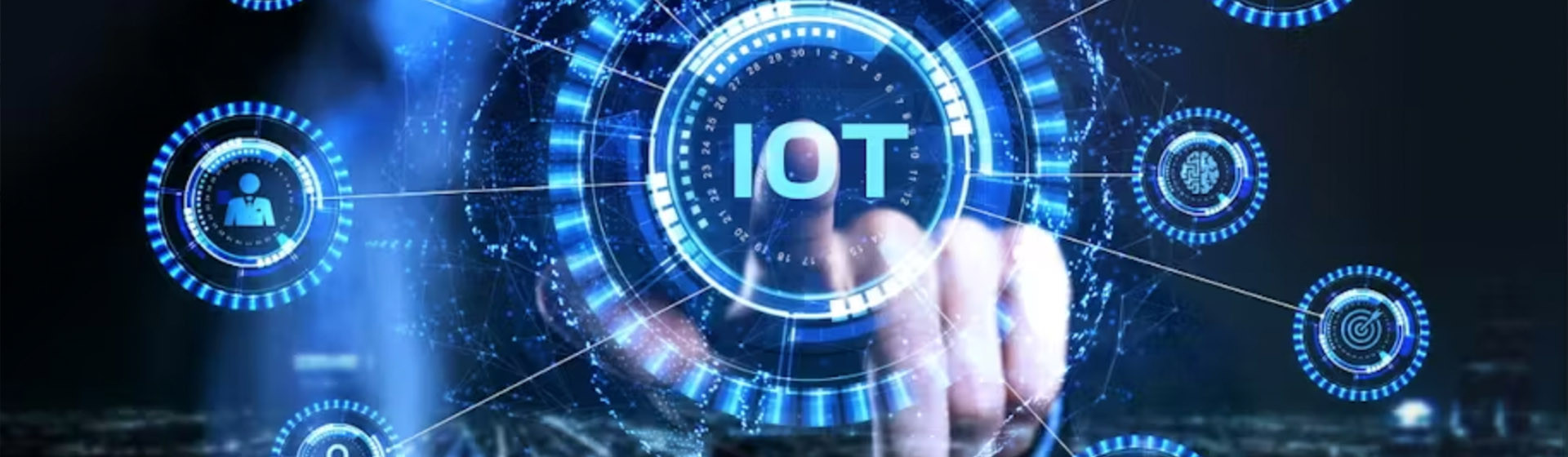
The integration of IoT (Internet of Things) technology into coil feed lines has become a game-changer for automotive manufacturers. Through IoT-enabled monitoring systems, real-time data collection on critical parameters such as feed speed, coil tension, and machine performance is now possible. This technology helps operators monitor and optimize machine performance, ensuring minimal downtime and early detection of issues before they cause production delays.
Key features of IoT monitoring include:
* Predictive maintenance capabilities that reduce the risk of unexpected failures.
* Remote access to machine performance data, allowing for faster troubleshooting and decision-making.
* Real-time insights into system performance, enabling immediate adjustments to improve efficiency.
As the automotive industry moves toward Industry 4.0, the integration of IoT into coil feed lines enhances overall operational transparency and reliability.
3. Energy-Efficient Coil Feed Lines for Sustainability
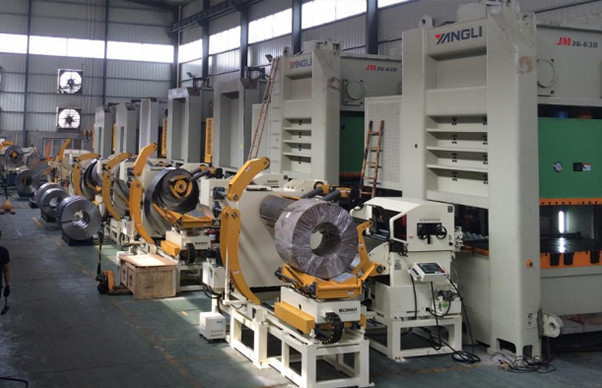
With a growing emphasis on sustainability, automotive manufacturers are increasingly adopting energy-efficient coil feed lines to minimize environmental impact and reduce operational costs. These systems are designed with advanced motors and regenerative technologies that optimize energy usage, allowing manufacturers to reduce their carbon footprint while maintaining high performance.
Energy-efficient coil feed lines offer:
* Reduced energy consumption, through the use of low-energy motors and regenerative braking.
* Lower operational costs, as energy savings contribute to cost reductions over time.
* Sustainability benefits, helping manufacturers meet environmental regulations and reduce emissions.
For manufacturers focused on meeting green manufacturing goals, energy-efficient coil feed lines provide a strategic advantage by aligning with eco-friendly practices without sacrificing productivity.
4. Modular Coil Feed Lines for Flexible Production
As automotive production becomes more complex with the introduction of electric vehicles (EVs) and autonomous driving technologies, modular coil feed lines are increasingly gaining popularity. These systems allow for quick adjustments to production setups, enabling manufacturers to switch between different product lines, materials, and configurations with ease. Modular systems can be customized with interchangeable components such as decoilers, straighteners, and feeders, providing greater flexibility and adaptability in a fast-paced production environment.
Advantages of modular systems include:
* Quick configuration changes to accommodate new product designs or materials.
* Scalability to support growing production demands.
* Customizability, allowing manufacturers to tailor feed lines to specific production needs.
Modular coil feed lines offer the flexibility needed for the modern automotive industry, where constant changes and upgrades are essential to staying competitive.
5. Integration with Robotic Systems for Enhanced Automation
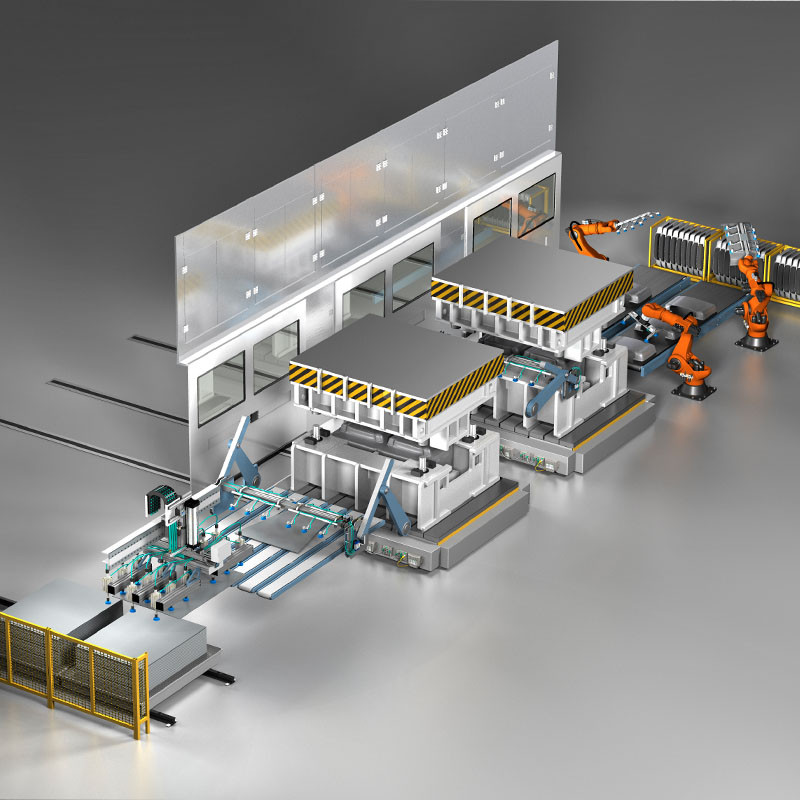
Automation is becoming a key factor in automotive manufacturing, and coil feed lines integrated with robotic systems are enhancing efficiency and precision. Robotic arms and automated handling systems work alongside coil feeders to manage coil loading, unloading, and material handling. This integration reduces the need for manual labor, improves workplace safety, and ensures greater precision in feeding materials to stamping and pressing machines.
Benefits of robotic integration:
* Reduced labor costs and improved safety through automation.
* Higher precision in material handling and coil feeding.
* Increased throughput with minimal downtime.
Automating the coil feeding process not only boosts efficiency but also supports the wider trend of increasing automation in automotive manufacturing.
Conclusion: The Future of Coil Feed Lines in the Automotive Industry
As we look ahead to 2025, coil feed lines will continue to evolve with a focus on precision, sustainability, and automation. Servo-driven systems, IoT integration, and energy-efficient solutions are leading the charge, offering manufacturers the tools they need to produce high-quality automotive parts faster, at a lower cost, and with less environmental impact. Investing in these innovations will be critical for manufacturers looking to remain competitive in an increasingly complex and demanding automotive market.