How to Overcome Common Challenges in Steel Coil Handling with Automation in 2025
Steel coil handling Equipment has long been a critical component of manufacturing in various industries, including automotive, aerospace, and metal fabrication. As demand for precision, efficiency, and cost-effective solutions continues to rise, the challenges faced in steel coil handling become more complex. However, with advancements in coil handling automation, businesses can now effectively address these challenges while optimizing their operations.
In this article, we’ll dive into the common challenges encountered in steel coil handling and explore how automated coil processing, coil handling systems, and industrial automation solutions can help overcome these issues in 2025.
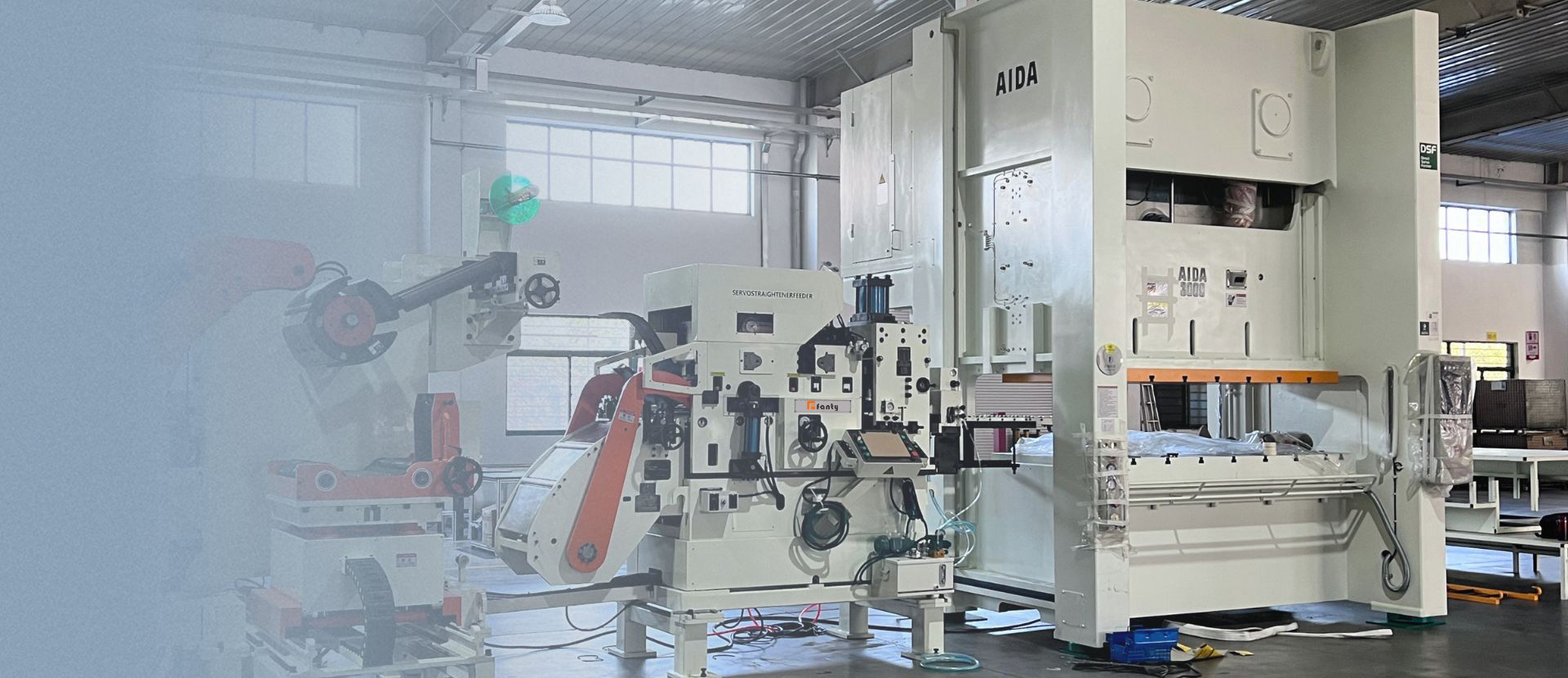
Key Challenges in Steel Coil Handling
1, Safety Hazards
Handling steel coils manually presents significant safety risks, such as the potential for injuries caused by the heavy weight, sharp edges, and the need for complex maneuvers during transportation.
2, Inefficient Workflow
Manual handling processes often lead to bottlenecks, delays, and poor material flow within a production environment. These inefficiencies reduce overall productivity and increase operational costs.
3, Inconsistent Quality
Manual processes are susceptible to human error, which can result in inconsistent coil positioning, misalignment, or improper handling. This can affect the quality of the product, especially when precision is critical.
4, Space Constraints
Steel coils can be bulky and heavy, requiring significant storage space. Managing and transporting coils within a limited space poses logistical challenges that can slow down production lines.
How Automation Solves These Challenges
1, Enhanced Safety with Automated Systems
Automated coil handling systems eliminate the need for manual lifting and transporting, significantly reducing the risk of injuries. Robotic arms, conveyors, and automatic coil positioning systems ensure that steel coils are safely and accurately handled throughout the production process.
2, Improved Efficiency with Smart Technology
Automation streamlines the entire steel coil handling process, from loading and unloading to uncoiling and positioning. Integrated sensors and smart controllers allow for faster, more precise handling, eliminating downtime and increasing throughput. This leads to improved workflow and productivity.
3, Consistent Quality through Precision Automation
Automated systems provide precise and repeatable handling, ensuring that coils are positioned correctly and consistently. The use of advanced robotics and automated feeding systems ensures that products meet the highest quality standards.
4, Space Optimization with Automated Storage and Retrieval Systems
Automated coil handling solutions, such as automated guided vehicles (AGVs) and robotic arms, allow for more efficient use of available space by optimizing coil storage and retrieval. This minimizes the need for extensive storage areas and increases space utilization, leading to more efficient operations.
The Future of Steel Coil Handling in 2025
In 2025, the evolution of coil handling automation will continue to push the boundaries of efficiency and safety in industrial environments. As manufacturing processes become more advanced, automation solutions will integrate seamlessly with other elements of production, including stamping and forming systems, to create fully automated production lines. As these technologies become more affordable and accessible, they will become increasingly common across industries worldwide.
Conclusion
Adopting automation for steel coil handling is no longer an optional upgrade for manufacturers; it is a necessity in today's fast-paced, competitive environment. By addressing common challenges such as safety, workflow inefficiencies, quality control, and space management, automated steel coil handling systems provide a practical solution for improving operational efficiency, reducing costs, and enhancing product quality. Companies that embrace these innovations will be better positioned for success in 2025 and beyond.