How to Choose the Right Stamping Automation Equipment for Your Production Line in 2025 ?
In the fast-evolving world of stamping automation, selecting the right stamping automation equipment for your production line is crucial for maintaining efficiency, precision, and cost-effectiveness. As manufacturers increasingly integrate automated stamping systems, servo presses, and coil feeding technology to optimize production, the demand for advanced solutions continues to rise. Choosing the right equipment requires careful evaluation of several factors, from production volume to material handling capabilities. This guide provides a detailed breakdown of how to select the best stamping automation equipment tailored to your manufacturing needs in 2025.
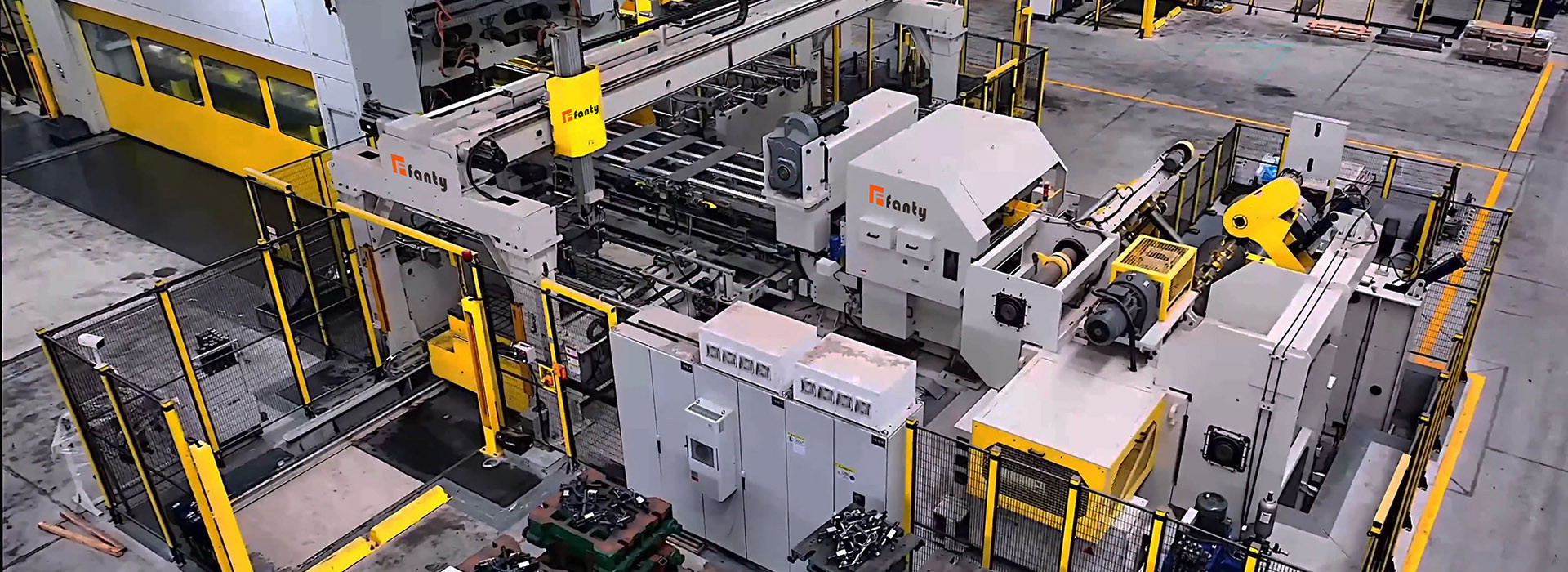
1. Understand Your Production Requirements
Before investing in stamping automation equipment, assess your specific production needs, including:
Production Volume: High-speed presses and fully automated coil handling systems are essential for mass production, while lower-volume runs may benefit from flexible servo-driven solutions.
Material Type: Whether working with stainless steel, aluminum, or high-strength alloys, different materials require specific press force and feeding mechanisms.
Part Complexity: For intricate components, precision stamping equipment with servo control ensures accuracy and repeatability.
Matching the equipment specifications to your production requirements will help maximize efficiency and reduce operational costs.
2. Choose the Right Stamping Press
The stamping press is the heart of any automation system. Depending on your application, consider the following types:
Mechanical Presses: Best suited for high-speed operations requiring consistent force and precision.
Hydraulic Presses: Ideal for deep drawing and forming applications where controlled pressure is needed.
Servo Presses: Offer superior control over speed, force, and positioning, making them ideal for complex stamping operations.
In 2025, servo-driven stamping presses are expected to dominate the industry due to their energy efficiency, flexibility, and enhanced process control.
3. Optimize Coil Handling and Feeding Systems
A well-integrated coil handling system is essential for maintaining continuous production and reducing material waste. Key components include:
Decoilers: Ensures smooth unwinding of coil material without causing deformation.
Straighteners: Corrects material curvature to ensure accurate feeding into the press.
Servo Feeders: Precisely controls material flow to match press timing, reducing scrap and improving efficiency.
Investing in automated coil feeding technology enhances precision, reduces downtime, and prevents misalignment issues in high-speed stamping operations.
4. Ensure Compatibility with Automation and Robotics
Modern stamping automation equipment integrates seamlessly with robotic handling systems for improved productivity. Consider automation features such as:
Automated Part Transfer: Reduces manual intervention and ensures consistent cycle times.
Robotic Pick-and-Place Systems: Enhances speed and accuracy in handling stamped parts.
Real-Time Monitoring and Data Integration: IoT-enabled presses provide real-time analytics for predictive maintenance and efficiency tracking.
By selecting stamping automation equipment that supports Industry 4.0 technology, manufacturers can optimize production, reduce downtime, and improve overall process reliability.
5. Evaluate Safety and Maintenance Requirements
Ensuring worker safety and minimizing machine downtime are critical when choosing stamping equipment. Look for:
Built-in Safety Features: Light curtains, emergency stop mechanisms, and automatic fault detection prevent workplace accidents.
Predictive Maintenance Technology: AI-driven sensors detect early signs of wear and alert operators before failures occur.
Easy Access for Maintenance: Equipment with modular designs simplifies servicing and minimizes disruptions to production.
Investing in equipment with enhanced safety and maintenance features helps manufacturers maintain long-term efficiency and regulatory compliance.
6. Consider Scalability and Future Expansion
As production demands evolve, investing in scalable stamping automation equipment ensures long-term flexibility. Consider:
Modular Systems: Easily upgrade or expand production capacity without significant downtime.
Multi-Purpose Tooling: Adaptable stamping presses that accommodate various die sets for diverse applications.
Advanced Control Systems: User-friendly interfaces and programmable settings make it easier to adjust for new product lines.
A forward-thinking approach to equipment selection enables manufacturers to scale operations efficiently while keeping pace with technological advancements.
Conclusion
Choosing the right stamping automation equipment for your production line in 2025 requires careful consideration of production volume, material compatibility, automation capabilities, and future scalability. By integrating automated stamping systems, servo presses, and coil handling solutions, manufacturers can achieve higher precision, improved efficiency, and lower operational costs.
With the rapid advancements in smart manufacturing, investing in high-performance stamping automation equipment ensures long-term competitiveness in the ever-evolving industrial landscape. Whether upgrading an existing system or setting up a new production line, selecting the right technology is key to maximizing productivity and profitability.